Silicon carbide mechanical seals offer excellent thermal conductivity and wear resistance
Author:admin Date:2023-05-06
Silicon Carbide Seal
Silicon carbide is a durable ceramic material that is often used in the production of seals. This material offers many advantages, which include great wear resistance, high-temperature resistance, and good chemical corrosion resistance. These characteristics make silicon carbide mechanical seals ideal for the harshest industrial applications.
Silicon carbide is available in both reaction-bonded and sintered forms. Reaction-bonded silicon carbide has higher tribological properties and provides greater stiffness and strength. However, it is susceptible to caustic environments and may cause premature seal failure. Sintered silicon carbide has no free graphite and is more abrasion resistant. The silicon carbide seal face is also very thermally conductive.
In addition to its high-performance properties, silicon carbide is light in weight and has a very high modulus of elasticity. This results in less distortion and helps reduce the amplitude of thermal shock. Furthermore, silicon carbide has a lower coefficient of friction than tungsten carbide.
For many years, tungsten carbide was the preferred choice for sealing applications. It has the highest tensile strength of any popular seal ring material and is well-suited to high-pressure applications. Although it is still preferred for certain applications, it has lost its place to newer materials.
Graphite-loaded silicon carbide materials have emerged as the choice for applications requiring high pressure and pressure velocity. Unlike tungsten carbide, the lubrication of a silicon carbide face is controlled by the amount of binder present. While a small amount of lubricant can improve tribological characteristics, most applications do not require a substantial lubricant to perform adequately.
The silicon carbide seal ring can be machined with spherical micropores using laser processing to enhance the seal's friction reduction performance. As a result, a seal ring made with this material can greatly reduce the friction coefficient. Additionally, the face is scratch-resistant and has minimal wear. Therefore, it is a good option for sealing gas or liquids.
Seal faces are very important components. When choosing a seal, it is critical to choose the right material for each application. Ceramic and silicon carbide materials are the ideal choices. They offer excellent chemical, abrasion, and temperature resistance as well as high tensile strength and abrasion resistance. Abrasion-resistant seals are especially recommended for applications that experience frequent or continuous wear.
In addition to their high tensile strength and abrasion-resistant characteristics, silicon carbide mechanical seals have excellent thermal conductivity and wear resistance. Their low coefficient of friction and low thermal expansion make them suitable for extreme temperatures. Moreover, these seals can be specified for high-frequency and voltage applications.
There are several different grades of silicon carbide available. Some of the best-performing materials are Alpha Sintered Silicon Carbide, graphite-loaded SiC, and GLSC. Each of these offers unique benefits.
For applications that experience frequent or continuous wear, such as pumping systems, silicon carbide impregnated with graphite can provide an effective lubricating property. Furthermore, a graphite-loaded SiC mechanical seal can help reduce warranty claims. Also, a siC-graphite combination can improve the tribological consistency of the seal.
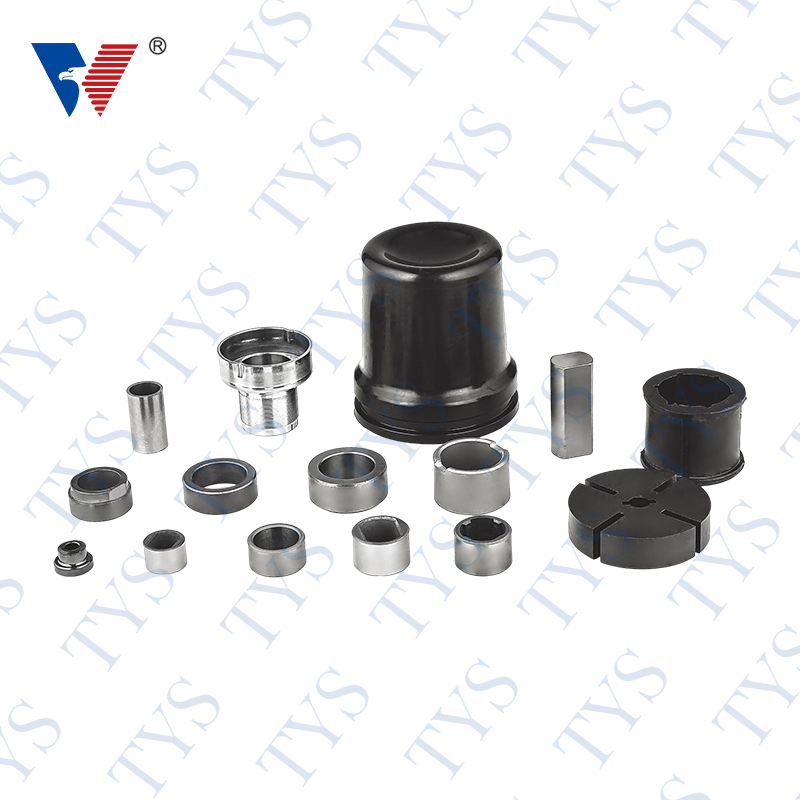
Silicon Carbide, Tungsten Carbide Technical Parameters
Item |
Unit |
Parameter |
|||
SSIC |
SSIC+G |
SSIC+V |
SSIC+M |
||
Voume Density |
g/cm |
≥3.10 |
≥2.80~3.05 |
≥2.95 |
≥2.70 |
%Porosity% |
% |
≤0.2 |
≤0.5 |
≤5 |
≤5 |
Hardness |
HRA/HS |
≥92(HRA294) |
≥91(HRA294) |
||
Bending Strength |
MPa |
≥400 |
≥190 |
≥150 |
≥120 |
Elastic Modulus |
GPa |
≥418 |
≥350 |
≥325 |
≥195 |
Compressive Strength |
MPa |
>2500 |
>1600 |
>1500 |
>900 |
Thermal Expansion Coefficient |
10/℃ |
4 |
3.0 |
2.6 |
2.5 |
Content of Sic |
% |
≥98 |
≥92 |
≥97.5 |
≥90 |
Temperature |
℃ |
1400 |
1400 |
1400 |
1400 |