Understanding a Vertical Pump Seal
Author:admin Date:2022-07-25
When considering a Vertical Pump Seal, it's important to understand its design and what causes problems. A mechanical seal consists of a rotating face and stationary face that are attached to the pump's shaft. While the two faces are in contact only when the pump is stationary, the fluid inside the pump must be lubricated to prevent liquid leakage. The seal's flexible "boots" are made of elastomer, flexible metal bellows. The lubricating liquid is used to reduce friction and aid in heat dissipation, as the pump rotates.
A vertical turbine mechanical seal is installed in the shaft column above the mounting plate. Fluid from the discharge exits the pump through the discharge nozzle, reducing the seal chamber's pressure. The seal's design allows the process fluid to circulate in the shaft column to minimize axial loading. To minimize axial load on the impeller, wear rings are used to reduce the differential pressure between the seal chamber and the pump casing. The seal chamber pressure is often equal to the pump's discharge pressure, which makes it important to have a flush port as high as possible on the shaft column.
API Plan 13 specifies the piping plans for pumps. The seal chamber must have a drainage port for the fluid that is used to lubricate the seal. The seal chamber pressure must be maintained in a range of 80 psi, as high pressures can damage the seal and reduce its efficiency. The pressure within the seal chamber is determined by the pump's equipment and process conditions. If the pump isn't pressurized, the seal may fail prematurely.
An abrasive liquid or abrasive gas may be trapped between the seal's stationary and moving parts. A lubricant will not cause leakage in this case. A pump with a gas seal, on the other hand, will protect the pump and its motor. When the pump fails to meet the specifications, it must be replaced. However, a seal with a good gas seal can prevent such a problem from occurring.
A mechanical seal's longevity depends on its type and environment. Understanding the needs of vertical pumps is important for extending its mean time between failures. In this article, we'll explore how a Vertical Pump Seal differs from conventional seals. In this article, we'll explain how the vertical pump's design and seal eliminate the packing problem that plagues many pumps. If you're planning on replacing your pump, contact an expert today!
A mechanical seal is far less expensive than a hydraulic one. The mechanical seal is more forgiving than its hydraulic counterpart, and it can accept large shaft movements and particles. This means that it can still work even after excessive wear and tear. The benefits of a mechanical vertical pump seal are that they are suitable for most applications. This is especially useful for cleaning liquids and recirculating them. A hydraulic pump, however, is not suitable for cleaning liquids because of the risk of chemical spills.
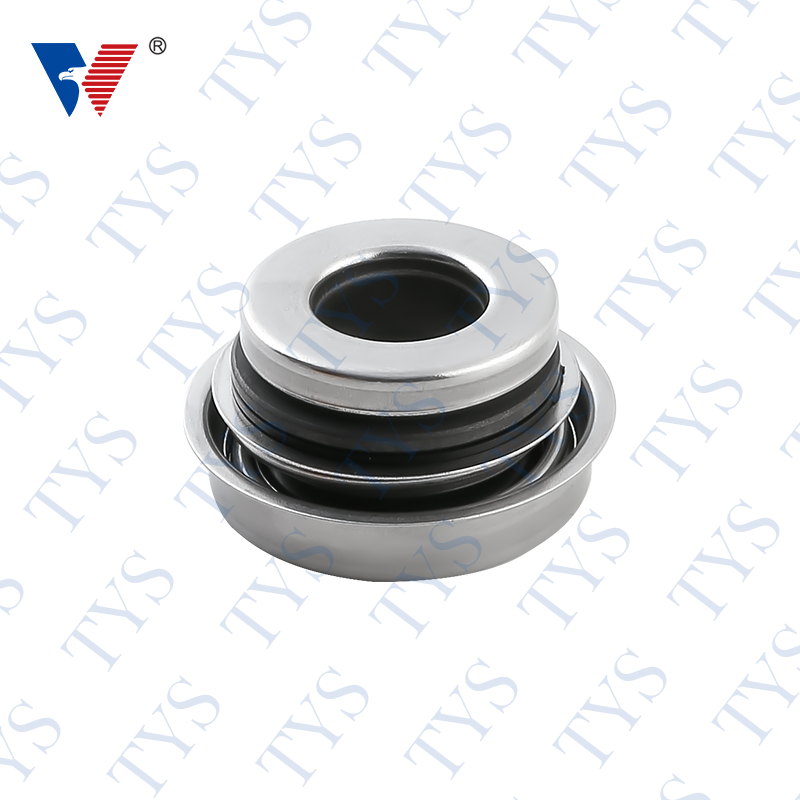
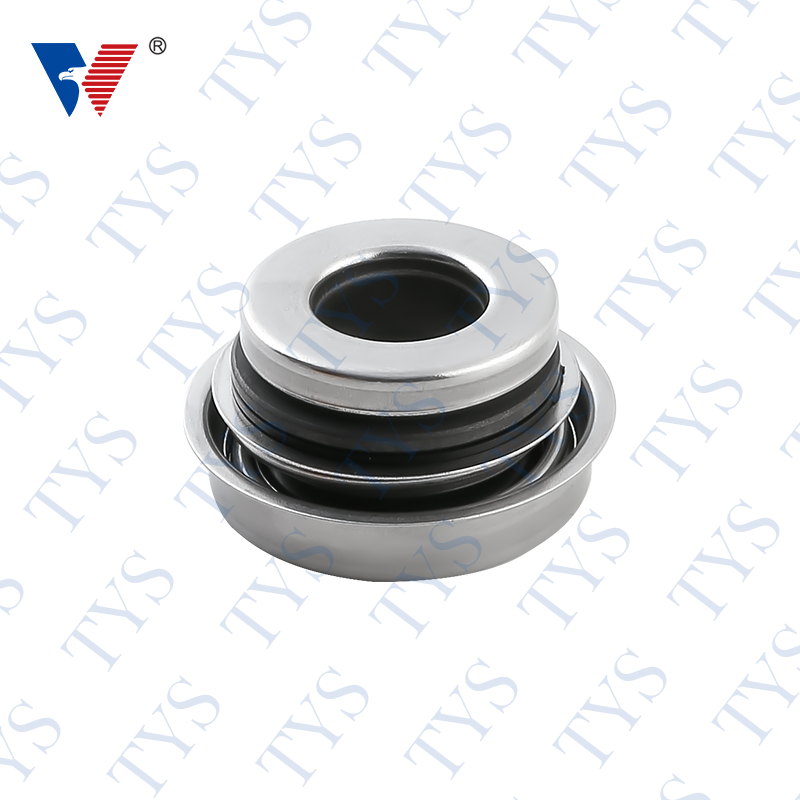