Types of Pump Mechanical Seals
Author:admin Date:2022-11-23
There are several types of pump mechanical seals. These include the Cartridge seal, Pusher seal, Outside seal, and segmented bushings. Identifying the type of seal you need is essential to ensuring your pump's efficiency and long-term reliability. Fortunately, mechanical seal problems are fairly simple to fix and can be quickly remedied.
Cartridge seal
The advantages of cartridge seals over packing are obvious. They offer a low power consumption and are simple to install. In addition, they avoid the need for subsequent adjustment. They can withstand high pressures up to 16 bar and a high surface speed of 30 m/s. In fact, most seals in service today are cartridge-type. The reason for this is simple: they contain all of the necessary components in one package. The two elements meet on the wear face and are precisely machined, which minimizes leakage.
Another major advantage of cartridge seals is that they are easier to install, reducing downtime associated with replacement. The seals are assembled in a factory, eliminating the need for manual adjustment. They also eliminate the risk of damaged shafts and other pump components.
Pusher seal
A pusher seal is a mechanical seal used on pumps. Its primary sealing ring is stationary while the secondary seal moves axially along the shaft. This arrangement allows the sealing liquid to be forced across the seal face without leakage. This type of mechanical seal is the least expensive. However, it is susceptible to abrasion, erosion, and wear.
The seal hardware includes a drive mechanism. This prevents rotational and axial slippage. The drive mechanism must be designed to withstand torque from the seal faces and axial thrust produced by the hydrostatic pressure. A number of different types of drives are available for this purpose.
Outside seal
Pump mechanical seals can either be internal or external. Internal mechanical seals prevent water from escaping the pump's casing and allow the pump shaft to spin freely. An internal mechanical seal is more reliable and complex than an external one. Both types have similar purposes but differ in design and functionality. The differences between internal and external seals include their design and installation.
Mechanical seals must be flushed with a liquid to prevent leakage. This liquid can be a waste product. The leaking of a mechanical seal can lead to secondary problems and extra cleaning and disposal costs. Unlike mechanical seals, gaskets don't need to be replaced as often and can be used in extreme wear and tear applications.
Segmented bushings
Segmented bushings for pump mechanical seals have several advantages over their traditional counterparts. For example, the seals can be retrofitted to incorporate gas barrier technology. As a result, leakage is minimized and the useful life of the packing is extended. The seals are available in various configurations, from simple, single point to multiple port designs.
Segmented bushings have large circulating grooves, which minimize the plugging of solids media within the seal. They also offer superior performance in stuffing boxes. Flowserve's virtual plant simulation tool lets you explore the capabilities of these seals in key industrial applications.
Cofferdams
The Cofferdam Pump Mechanical Seal is an essential component of a pump system. This type of seal is used for both water and wastewater applications. Unlike many other types of pumps, this type of seal can withstand high pressures without leaking. Because it is so sensitive, it requires careful engineering and design.
There are two types of mechanical seals for cofferdams. The first one has a mechanical seal which helps prevent it from leaking. This seal prevents infiltration and piping. Cofferdams must be set at a distance away from open excavations. Foundation treatments include in situ compaction, deep penetration of sheet piling, and the use of blankets and berms. Foundation material consolidation, such as grouting, is also used.
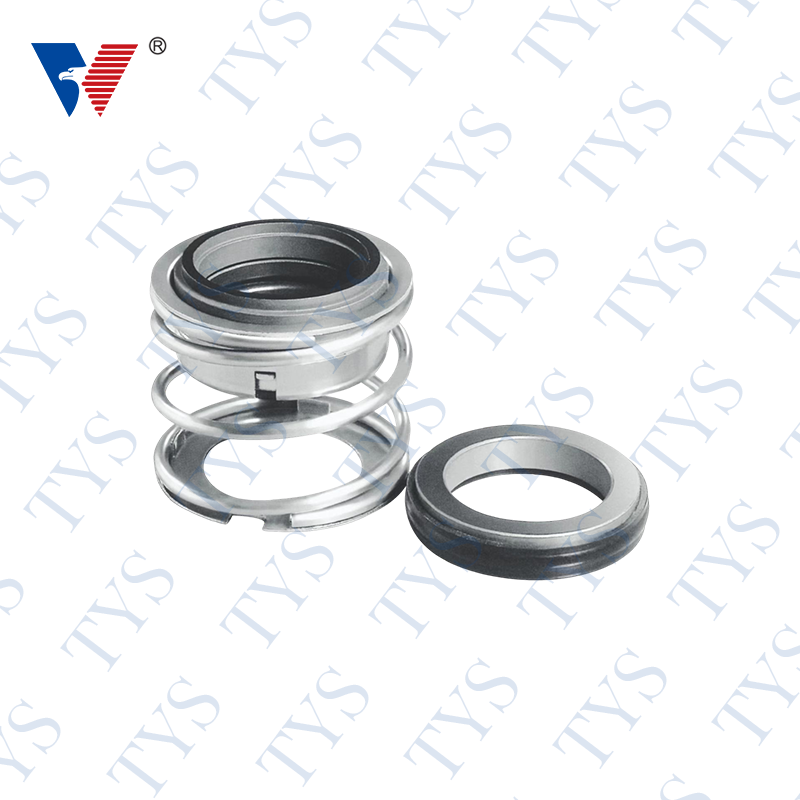
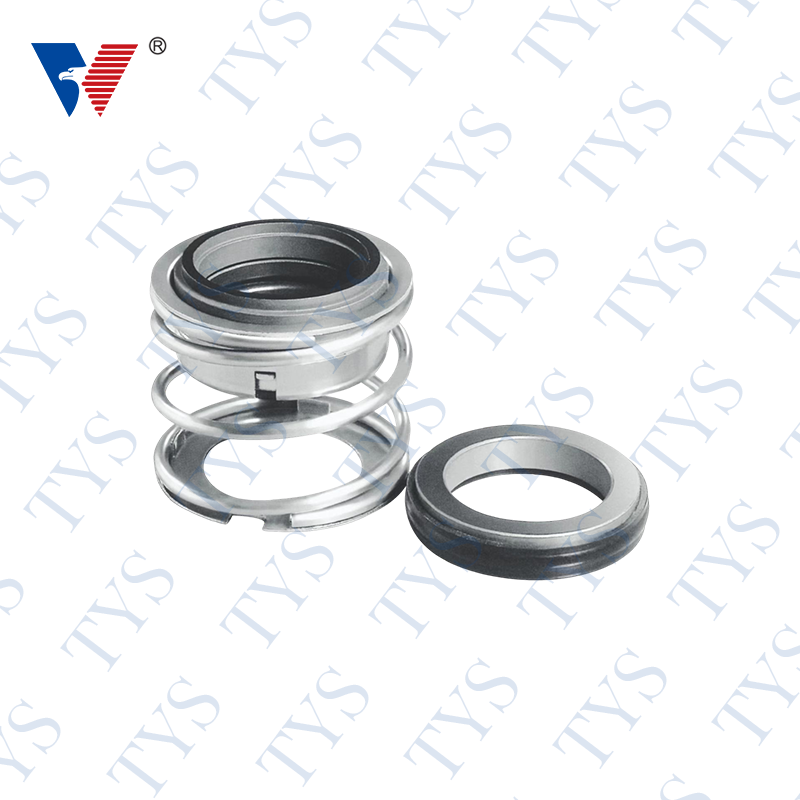
TYS B2 Mechanical seal for CNP Horizontal single stage centrifugal pump
MODEL | d1 | d3 | d4 | D7 | D12 | L | L3 | L4 | L5 | L6 |
16 | 16 | 34 | 37 | 30 | 5 | 33 | 25 | 8 | 1.2 | 6 |
18 | 18 | 36.8 | 40 | 32 | 5 | 33 | 25 | 8 | 2 | 6 |
20 | 20 | 38.8 | 42 | 34 | 5 | 33 | 25 | 8 | 2 | 6 |
B2-22 | 22 | 41.5 | 45 | 36 | 5 | 33 | 25 | 8 | 2 | 6 |
B2-25 | 25 | 44.8 | 48 | 39 | 5 | 34 | 26 | 8 | 2 | 6 |
B2-28 | 28 | 48.5 | 52 | 43 | 5 | 34 | 26 | 8 | 2 | 6 |
B2-30 | 30 | 52 | 55 | 48 | 5 | 34 | 26 | 8 | 2 | 7 |
B2-35 | 35 | 57 | 60 | 53 | 5 | 40 | 30 | 10 | 2 | 8 |
B2-40 | 40 | 67 | 70 | 58 | 5 | 44 | 34 | 10 | 2 | 8 |
B2-45 | 45 | 73 | 76 | 63 | 5 | 46 | 36 | 10 | 2 | 8 |
B2-50 | 50 | 79 | 81 | 68 | 8 | 51 | 41 | 10 | 2 | 8 |
B2-55 | 55 | 84 | 87 | 73 | 8 | 53 | 41 | 12 | 2.5 | 10 |
B2-60 | 60 | 90 | 95 | 79 | 8 | 53 | 41 | 12 | 2.5 | 10 |
B2-65 | 65 | 98.5 | 104 | 86 | 8 | 61 | 49 | 12 | 2.5 | 10 |
B2-70 | 70 | 103.5 | 109 | 91 | 8 | 64 | 52 | 12 | 2.5 | 10 |
B2-75 | 75 | 110.5 | 116 | 96 | 8 | 64 | 52 | 12 | 2.5 | 10 |
B2-80 | 80 | 120 | 125 | 105 | 11 | 70 | 56 | 14 | 3 | 12 |
B2-85 | 85 | 125 | 130 | 110 | 11 | 70 | 56 | 14 | 3 | 12 |
B2-90 | 90 | 132 | 137 | 115 | 11 | 70 | 56 | 14 | 3 | 12 |
TYSB2-95 | 95 | 137 | 142 | 120 | 11 | 70 | 56 | 14 | 3 | 12 |
TYSB2-100 | 100 | 144 | 149 | 125 | 11 | 70 | 62 | 14 | 3 | 12 |
MODEL | d1 | d3 | d4 | D7 | D12 | L | L3 | L4 | L5 | L6 |
TYSB2-3/8" | 9.52 | 28 | 32 | 24.6 | 5 | 33.7 | 25 | 8.7 | 1.5 | 6 |
TYSB2-1/2" | 12.7 | 32 | 35 | 27.8 | 5 | 33.7 | 25 | 8.7 | 1.5 | 6 |
TYSB2-5/8" | 15.87 | 34 | 39 | 30.95 | 5 | 35.3 | 25 | 10.3 | 1.5 | 6 |
TYSB2-3/4" | 19.05 | 38.8 | 43 | 34.15 | 5 | 35.3 | 25 | 10.3 | 2 | 7 |
TYSB2-7/8" | 22.22 | 41.5 | 46 | 37.3 | 5 | 35.3 | 25 | 10.3 | 2 | 7 |
TYSB2-1" | 25.4 | 44.8 | 50 | 40.5 | 5 | 35.3 | 25 | 10.3 | 2 | 7 |
TYSB2-1 1/8" | 28.57 | 48.5 | 59 | 47.65 | 5 | 44.9 | 33 | 11.9 | 2 | 7 |
TYSB2-1 1/4" | 31.75 | 57 | 62 | 50.8 | 5 | 44.9 | 33 | 11.9 | 2 | 7 |
TYSB2-1 3/8" | 34.92 | 57 | 66 | 54 | 5 | 44.9 | 33 | 11.9 | 2 | 7 |
TYSB2-1 " | 38.1 | 67 | 70 | 57.15 | 5 | 44.9 | 33 | 11.9 | 2 | 7 |
TYSB2-1 5/8" | 41.27 | 67 | 74 | 60.35 | 5 | 44.9 | 33 | 11.9 | 2 | 7 |
TYSB2-1 3/4" | 44.45 | 73 | 77 | 63.5 | 5 | 52.9 | 41 | 11.9 | 2 | 7 |
TYSB2-1 7/8" | 47.62 | 73 | 81 | 66.7 | 5 | 52.9 | 41 | 11.9 | 2 | 7 |
TYSB2-2" | 50.8 | 79 | 85 | 69.85 | 8 | 54.5 | 41 | 13.5 | 2.5 | 10 |
TYSB2-2 1/8" | 53.97 | 84 | 88 | 73.05 | 8 | 54.5 | 41 | 13.5 | 2.5 | 10 |
TYSB2-2 1/4" | 57.15 | 84 | 91 | 76.2 | 8 | 54.5 | 41 | 13.5 | 2.5 | 10 |
TYSB2-2 3/8" | 60.32 | 90 | 94 | 79.4 | 8 | 54.5 | 41 | 13.5 | 2.5 | 10 |
TYSB2-2 1/2" | 63.5 | 94 | 97 | 82.55 | 8 | 54.5 | 41 | 13.5 | 2.5 | 10 |