Tips For Selecting a Mechanical Seal
Author:admin Date:2022-07-07
The most basic solution for a mechanical seal is to upgrade the faces of the mechanical seal. If the liquid being sealed is mildly abrasive, this is the easiest and cheapest option. The hard material used is silicon carbide, but other ceramics are available. However, silicon carbide can wear easily and build up heat during startup and shutdown. In addition, dry running can melt elastomeric parts, so this method is not recommended for all liquids.
A secondary seal is used to prevent fluid from leaking through areas that would otherwise be filled with fluid. These seals are usually flexible members that seal when deformed against the part being sealed. Most secondary seals use o rings, which are widely available and can be easily purchased. As the name suggests, secondary seals can be either stationary or rotating. If the abrasive medium is not a significant factor, a secondary seal can be used.
The selection of a mechanical seal is based on several factors, including the type of material used, operating conditions, and process conditions. Proper operation and design of the mechanical seal is important for stability, plant safety, and economic viability. Ultimately, selecting the right mechanical seal for your application will ensure your processes remain stable and productive. There are many factors to consider when selecting a mechanical seal. The following tips will help you make the best choice.
A mechanical seal is an important part of centrifugal pumps. This part of the pump is responsible for keeping the fluid contained within the impeller shaft. Various seal designs are available for almost every conceivable pumping process. These include seals for low-to-high fluid temperatures, clean plant water, and heavy hydrocarbons. Furthermore, seal support systems are available for every pumping process. This way, the mechanical seal can adapt to any pumping process.
Proper mechanical seal support systems are critical to the petroleum industry. They protect pumps from oxidation, reduce heat, and prevent leakage. And they deliver process fluid such as water, oil, or inert gas. Proper support systems reduce friction and heat while ensuring the correct operation of the seal chamber. Proper maintenance of these systems can prevent loss of profitable products, pump degradation, and environmental risk. These are all factors to consider before purchasing a mechanical seal.
Generally, a mechanical seal system has two parts: the rotating element attached to a rotating shaft with set screws or a clamp. The rotating element then turns against a stationary unit in a gland housing. Hydraulic pressure generated by the fluid being pumped and mechanical loading with springs help maintain continuous contact between the two parts. The mechanical seal prevents leakage along the shaft. There are two basic types of mechanical seals: the pusher and the non-pusher type.
Double seals are also available. A double-sided mechanical seal is designed to keep a pumped liquid from escaping into the outside. This arrangement allows for the introduction of a buffer fluid, or a pressurizing gas blanket to the seal. Both types of double seals are most commonly used in sealing volatile organic compounds, dirty products, and products that change state. It is important to note that a double seal will require a pressure maintenance pump.
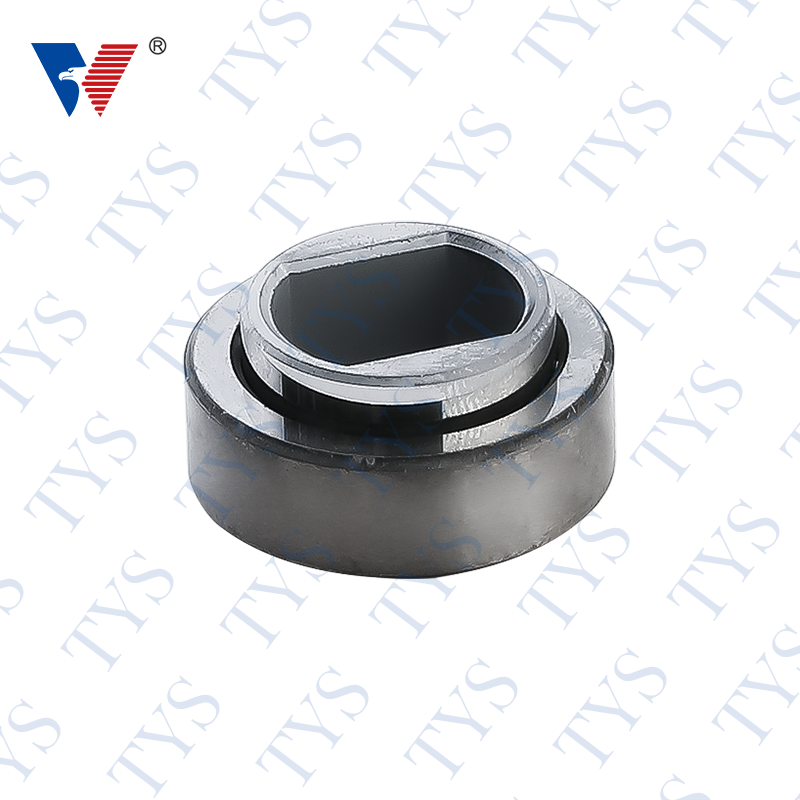
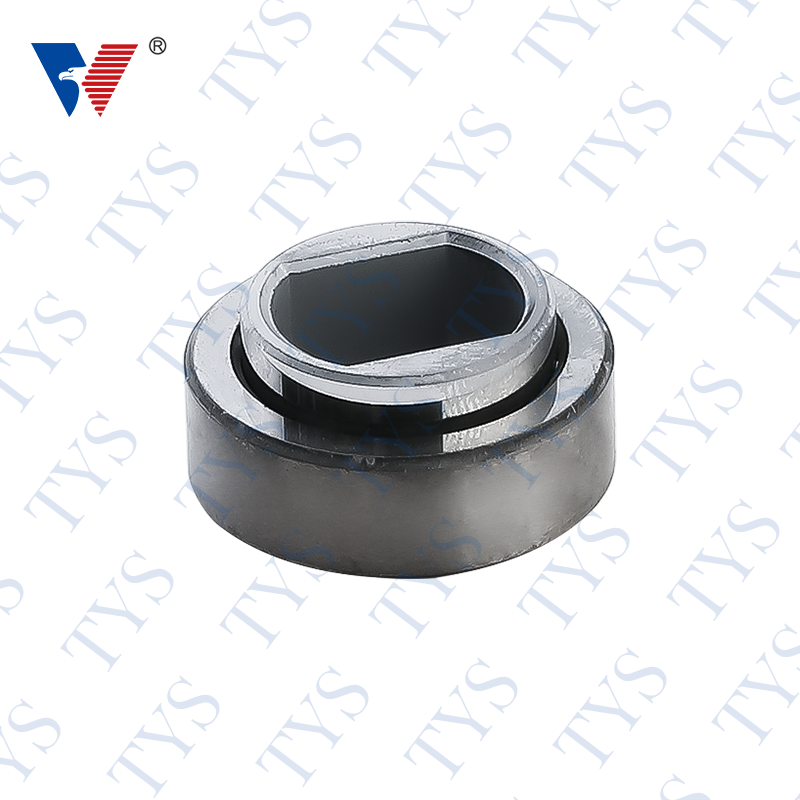