How to Change a Pump Mechanical Seal
Author:admin Date:2022-07-07
In order to maintain the performance of a Pump Mechanical Seal, it must be properly lubricated and cooled. The lubricant is generally a pumped product. This lubricant is injected into the chamber where the seal is installed. The pressure drop between the stationary and rotating elements determines leakage levels. Flow through an equivalent orifice is acceptable. The lubricant leakage rate can be calculated by comparing the pressure drop across the faces of the seal with the flow rate through the pump's main chamber.
Other factors that can lead to a Pump Mechanical Seal failure include: shaft misalignment, coupling imbalance, and bad base. Additionally, improper maintenance of bearings, couplings, and shafts can contribute to pump failure. In addition, vibrations may signal a leaking mechanical seal, and it is crucial to address any leaks as soon as possible. To reduce the risk of repeat leakage, check the shaft and ensure that it is not leaking.
When inspecting a Pump Mechanical Seal, take note of the installation procedure. A mechanical seal may be installed incorrectly, and a slight amount of grit on the faces can cause severe damage. On only one or two revolutions of the pump's speed, a contaminated seal can cause permanent damage. To avoid this, always ensure that the seal is clean before attempting to start the pump. And, remember that body oil, which can destroy mechanical seals, should not be used.
A Mechanical Seal is comprised of two flat surfaces that press against each other by a spring. A liquid film forms between the two surfaces. When the pump is running dry, the two surfaces are forced together and can cause frictional heat. This results in a failure of the Seal. When you replace the seal, you'll be saving yourself money and hassle. So, how do you change a Pump Mechanical Seal? Read on to learn more.
Depending on the application, Pump Mechanical Seals have different sealing points. Using a Gland Packing is one method of forming a seal. The packing physically stuffs the gap between the shaft and pump housing. Unfortunately, this packing can eventually be worn out by the friction of the shaft. Then, you'll have to adjust the packing to maintain the proper seal pressure. Another method is to use a gasket or o-ring as a static seal.
The most common mechanical seal design is a double seal. The difference between a double and single seal is in the direction that the product side seal rotates in the pumped fluid. This type of seal is prone to seepage, which results in contamination of the barrier lubricant and potentially damaging the atmospheric side seal. Another option is a cartridge seal, which contains the mechanical seal components in a preassembled package. The advantage of a cartridge seal is that it eliminates the installation issues of the mechanical seals. A tandem seal design may be a gland or built onto the sleeve.
When a single mechanical seal leak occurs, it's difficult to pinpoint the exact cause. The problem is often so subtle that the pump operator can't identify it without an expert inspection. If a single mechanical seal is leaking, you're best off modifying your system or repairing the problem before it becomes severe. A proper maintenance program will protect your pump and prevent future leaks. There are several ways to test a mechanical seal.
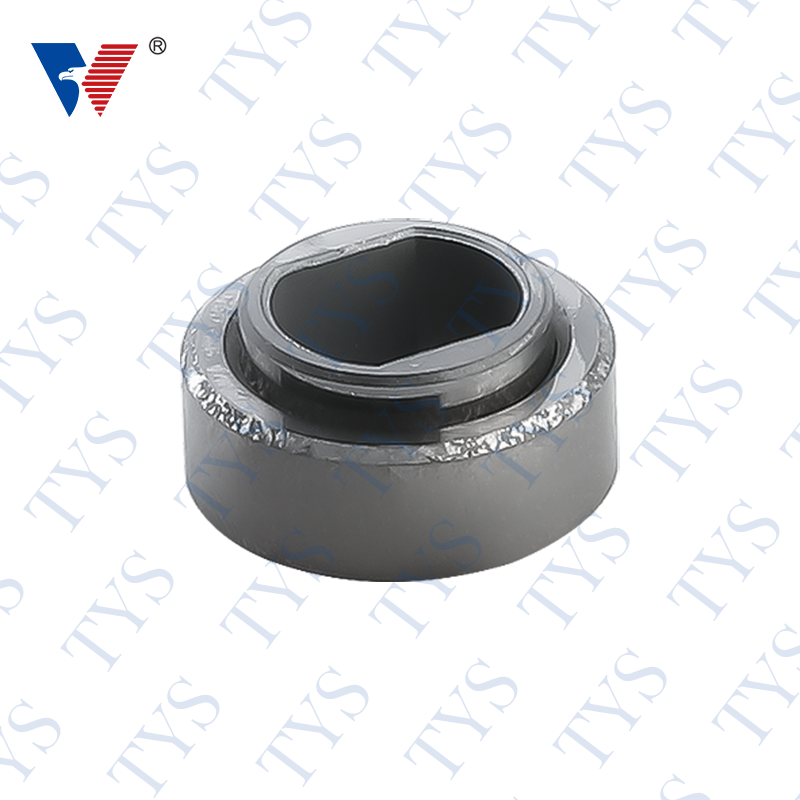
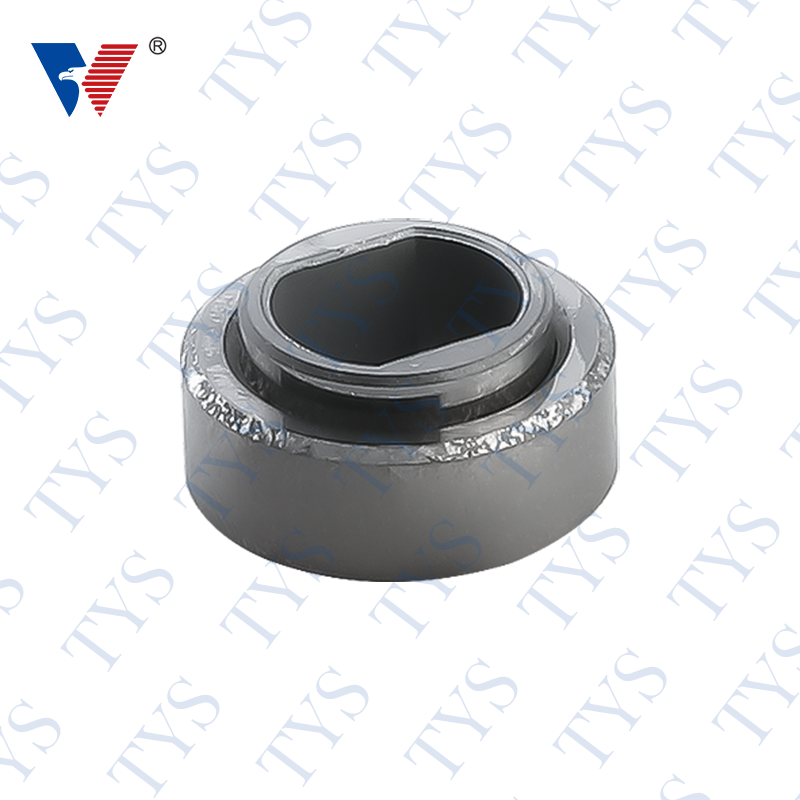