Rubber Mechanical Seal is one of the most comfortable seals to use in a wide variety of applications
Author:admin Date:2023-06-16
Designing a Rubber Mechanical Seal
Designed to be mounted with ease, the Rubber Mechanical Seal is one of the most comfortable seals to use in a wide variety of applications. The main application of this seal is the water, oil, and chemical industries. They are used for applications with high pressures, high temperatures, and corrosive mediums. The material of construction depends on the type of fluid.
Rubber mechanical seals can be manufactured as per the customer's specifications. The most common design is an o ring. The o ring is a gasket with a torus shape. It can be used for a variety of applications, including automobiles. It is available in many different sizes and can be purchased for less than a dollar a dozen.
When designing a seal, the manufacturer must consider several factors, including the pressure and temperature range of the application. They also need to take into account the relative motion of the parts. The materials of construction should be durable and free of machining defects. Using a zeolite or carbon blend in the rubber can improve the low temperature and frost resistance of the seal. The addition of a zeolite compound will also increase the absorption of additives.
The most important aspect of a mechanical seal is the sealing face. It can be manufactured from a variety of materials. These materials may include tungsten, ceramic, and low friction carbon. However, the final finish should be smooth. This helps to prevent the formation of a lubricating fluid film at the seal's interface. In addition, the smoother the finish, the lower the wear. This feature is especially important for mechanical seals in demanding applications.
When designing a mechanical seal, the designer should take into account the drive mechanisms that will be used to support spring like features. This allows the seal to self-adjust. The drive mechanism can be used to provide a uniform deflection across the seal's surface. Some designs have a four bolt design, which eliminates cocking of the gland. This design is especially useful in applications where the sealing face may have to be changed regularly.
Another important consideration is the relative motion of the seal. This will affect the performance of the seal. If the seal is not balanced, it will be unbalanced. An average unbalanced external seal is suitable for pressures up to 30 psig. If the seal is symmetrical, it should be able to handle pressures of up to 150 psig. Special designs can handle much higher pressures.
Choosing the right material of construction for your seal can be a difficult task. A seal manufacturer can help you choose elastomeric polymers that suit your specific application. They will also be able to tell you how to identify the chemistry of the sealed fluid.
The sealing element should be between 10 and 20 microinches. It is important to protect the sealing elements from sharp edges and tools. The elastomeric material should be able to withstand temperatures of at least -40 degrees Celsius. It should also be able to resist chemical attack.
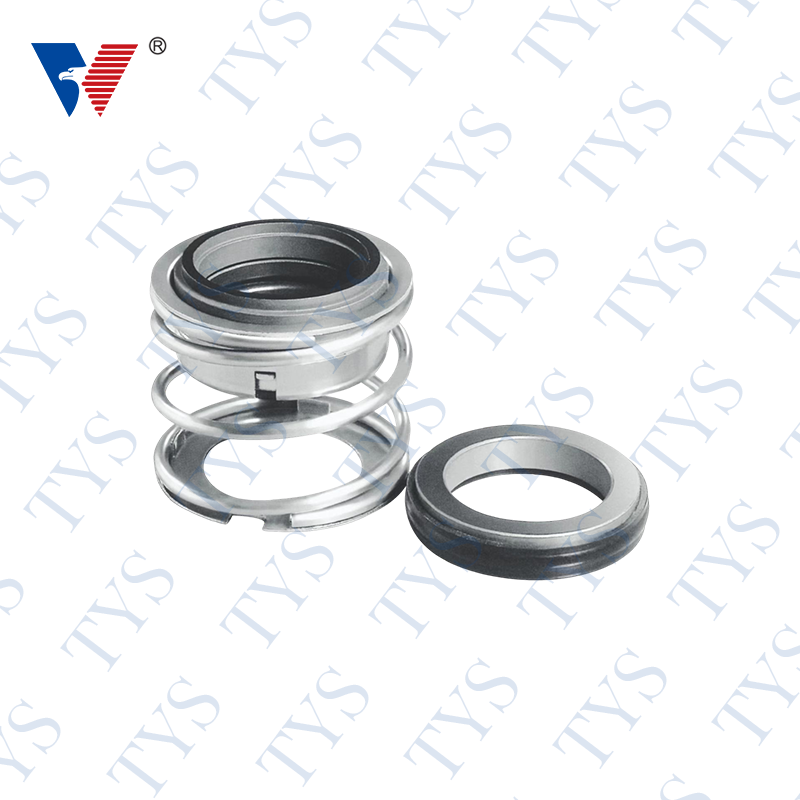
TYS B2 Mechanical seal for CNP Horizontal single stage centrifugal pump
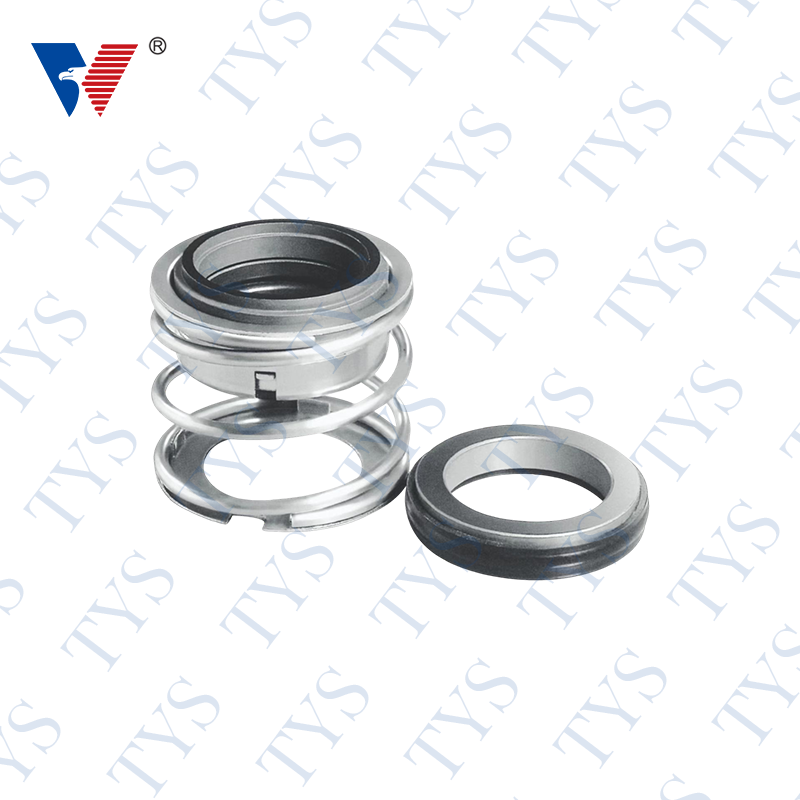
TYS B2 Mechanical seal for CNP Horizontal single stage centrifugal pump