How to Design a Rubber Seal
Author:admin Date:2023-03-15
How to Design a Rubber Seal
Whether you're putting together a home bathroom, a swimming pool pump system, or any other consumer application, there is a good chance you will need a Rubber Seal. These seals are used in a variety of applications and are able to adhere to many different types of surfaces. They are made from a range of materials, from a natural latex to artificial synthesis.
When designing a rubber seal, it's important to understand that the material you choose can make all the difference. The wrong material can lead to failure. You must know what type of seal you need, and the conditions in which it will be used. You can also choose from a wide variety of shapes and sizes. Often, it's best to use a seal with a cross-section that is larger than the gland's depth. This allows the seal to compress and seal without disrupting the connection between the mating surfaces.
For example, if you need to seal a gas tank, the seal must be able to withstand the pressure that will be exerted. The temperature of the gas should be considered when selecting the seal's material. If the seal is unable to withstand the temperature, it will become damaged. This can lead to cracking or leakage. It's possible to find a seal that can withstand temperatures of up to 480 degrees Fahrenheit. AFLAS(tm) is an excellent choice for heat resistance, and FiberFrax is another type of specialty seal.
The most common method of producing a custom Rubber Seal is extrusion. This process involves forcing molten rubber through a die, which creates a long profile. Other methods include injection molding, which is the process of shaping a part to fit its intended location. Non-extruded sealants are usually applied as liquids or gels. They are sometimes molded into shape, but the process isn't automated.
Several factors affect the performance of a rubber seal, including the size of the cross-section and the closing force. You should also consider how you plan to assemble the seal. Asymmetrical construction will decrease assembly time. However, too smooth a surface can lead to stick-slip effects in dynamic applications. For these reasons, a slightly rough surface is best.
You can also choose a seal with a memory function, which will return to its original state after the pressure is removed. This can be beneficial in high-temperature or dynamic applications and can help prevent leaks. It's important to test the seal's memory ability, though. If the seal is unable to retain its memory, it can cause trouble in future applications.
Some seals are a mixture of rubber and plastic. This can help you increase the durability of the seal, but can also result in a more expensive product. You can also choose from a variety of formulations of plastic, such as EPDM, which is lightweight and resistant to aging. It's also very easy to die-cut.
Rubber seals are available in a variety of forms and can be molded into a variety of shapes. They are used in many different industries, including swimming pools, HVAC systems, and kitchens. They are also found in a number of other applications, including weatherstripping and insulation.
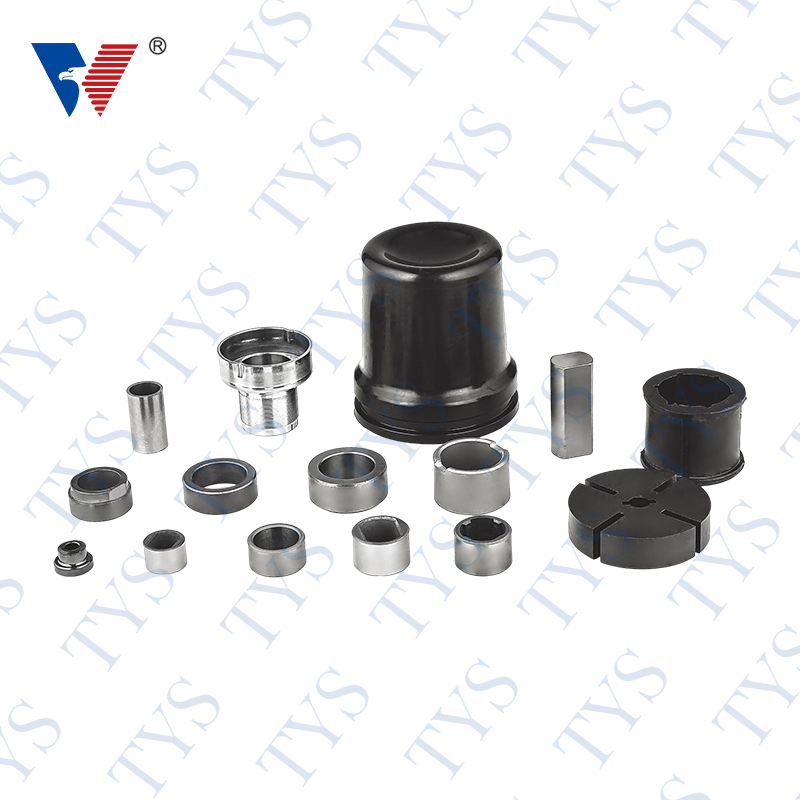
Silicon Carbide, Tungsten Carbide Technical Parameters
Item |
Unit |
Parameter |
|||
SSIC |
SSIC+G |
SSIC+V |
SSIC+M |
||
Voume Density |
g/cm |
≥3.10 |
≥2.80~3.05 |
≥2.95 |
≥2.70 |
%Porosity% |
% |
≤0.2 |
≤0.5 |
≤5 |
≤5 |
Hardness |
HRA/HS |
≥92(HRA294) |
≥91(HRA294) |
||
Bending Strength |
MPa |
≥400 |
≥190 |
≥150 |
≥120 |
Elastic Modulus |
GPa |
≥418 |
≥350 |
≥325 |
≥195 |
Compressive Strength |
MPa |
>2500 |
>1600 |
>1500 |
>900 |
Thermal Expansion Coefficient |
10/℃ |
4 |
3.0 |
2.6 |
2.5 |
Content of Sic |
% |
≥98 |
≥92 |
≥97.5 |
≥90 |
Temperature |
℃ |
1400 |
1400 |
1400 |
1400 |