Choosing the Right Centrifugal Pump Seal
Author:admin Date:2023-04-04
Using the right pump seal is important to avoid leaks and increase the efficiency of a centrifugal pump. Seals are designed to minimize the amount of process fluid reaching the atmospheric side of the seal. Choosing the right seal depends on the application, the nature of the fluid, and the operating conditions. Some applications require special seals that can be expensive or hard to install.
A mechanical seal is a simple device that can prevent leaks in a centrifugal pump. It contains several discrete parts and springs that work together to ensure the pump seal remains airtight. However, improper installation can cause seal damage and reduce seal life. If a mechanical seal is installed improperly, it can result in leaks, excessive vibration, and shaft play. This type of leak is caused by improper alignment of the mechanical seal or shaft.
The shaft seal usually involves friction and wear. The material used to create the seal is usually harder than the pumped liquid. This material wears slower with less friction. If the pumping process requires the shaft to move in a wet environment, friction will increase and wear out the shaft seal material.
The type of pump seal you choose depends on the type of liquid and the operating conditions. If the liquid is abrasive, upgrading the seal faces may be the best solution. In these cases, a hard material such as silicon carbide is recommended. This material can withstand wear and tear but can cause heat buildup during startup and shutdown. It is also susceptible to thermal shock.
If the pumping process involves flammable liquids, special flushing liquids and pumps will be required. The elastomer parts of a seal can melt and burn if they come in contact with high temperatures. The material used for this type of seal should be impregnated with carbon/graphite to help reduce the problem.
Some seals are designed to be installed with a simple piping plan. Other seals require a more complex design. These seals can be used in multiple stages for higher pressures. If a pump seal is installed improperly, it can cause leaks and damage other parts of the pump. These seals are commonly used in hygienic processing industries.
Seal faces must provide lubricity and withstand wear and tear. They are machined using the lapping process to ensure flatness. They are generally made of silicon carbide or other hard ceramic/metal materials. They can also be balanced for higher-pressure sealing. The faces can also be impregnated with carbon/graphite for dry running.
Seal faces are also used to modify the environment within a sealed chamber. If a pump seal is being used in a run-dry condition, the faces will become very hot. This increases the rotor rpm and can cause premature pump failure. The faces are also prone to abrasive particles, which are often dissolved in the liquid that comes out of the solution. If a pump seal is installed improperly, these particles can also wear out the seal faces and cause leaks.
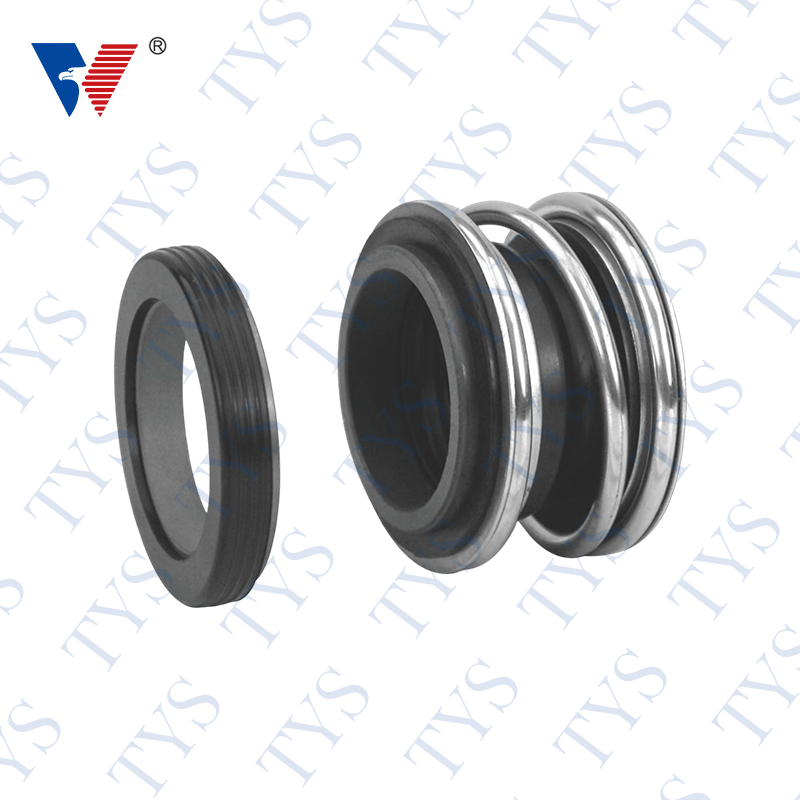
TYS1009、MG1、MG12、MG13 Rubber bellows mechanical seal professional mechanical seal supplier
Annular Seal Pressure: ≤0Mpa~1.2Mpa
Annular Seal Temperature: -20~80℃(-30~200℃)
Rotation speed: ≤12m/sec
Medium: Water, Oiland PH numerical value of waste wateris 6.5-8
Used in clean water pumps,in-Line pumps and general industrial pumps
- Mechanical Seals
- Single Face
- Single Spring
- Unbalanced Seal
- Arbitrary Rotation
- Stationary Ring(Ceramic/SiC/TC)
- Rotary Ring(Carbon/SiC)
- Secondary Seal(NBR/EPDM/VITON)
- Retainer(SUS304)
- Spring(SUS304)
- Spring Holder(SUS304)