Choosing the correct seal material is critical when constructing a rubber seal
Author:admin Date:2023-01-16
How to Construct a Rubber Seal
Choosing the correct seal material is critical when constructing a rubber seal. It is important to select the right material for the expected temperatures and climates of the application. In addition, it is critical to consider the size of the seal. If the cross-section is too small, the seal may not compress or may cause the connection between the mating surfaces to break. It is also important to avoid too smooth a surface. This may lead to stick-slip effects in dynamic applications.
Rubber sealing materials can be molded or extruded. They are typically shaped into long profiles and strips. They are processed through various thermoforming processes to create the desired shape. The most common method is injection molding, which involves forcing molten rubber through a die. In addition, they can be baked in the same way.
There are several different rubber compounds with different maximum temperature limits. If the material is exposed to extreme temperatures, it can cause cracking or permanent deformation. In order to choose the best seal material for your application, it is important to know the maximum temperature limit. The material should also be chosen based on the length of time that it will be exposed to the environment. If the temperature is too low, the material can be damaged and will not be able to hold up to the deformation pressure. In addition, if the seal is exposed to a temperature higher than the maximum limit, it can cause the material to shrink, which could result in leakage.
When designing a seal, it is important to consider the surface finish of the rubber material. This can affect the fluid containment of the fluid power application. In addition, it is a good idea to have a symmetrical construction to reduce assembly times.
It is also important to take into consideration the pressure that the seal will need to withstand. Depending on the seal, it can be made from rubber or plastic. When customizing the seal, it is also important to account for friction. If the seal will be used to provide a sliding connection, then the coefficient of friction is a critical factor. The seal should be designed with enough elasticity to withstand pressure.
Sealing applications can require a closing force of up to 20 pounds. During the process of compression, the seal may be permanently deformed. The rubber will return to its original shape when the stress is released. This is known as a compression set. It can occur during the production of the seal, or during a test.
If the seal is to be subjected to a large amount of force, the seal's memory function will need to be tested. It is not a universal test, but a company should use the test that they think is appropriate for their application. The Rubber Group uses drawing designations from the Association for Rubber Products Manufactures to help determine the performance requirements for a particular seal.
There are many different industries that employ rubber seals. These include medical, food, and pharmaceutical. They are a versatile product that can offer a quality solution to sealing problems. They are available in a variety of sizes and can be customized to meet your needs.
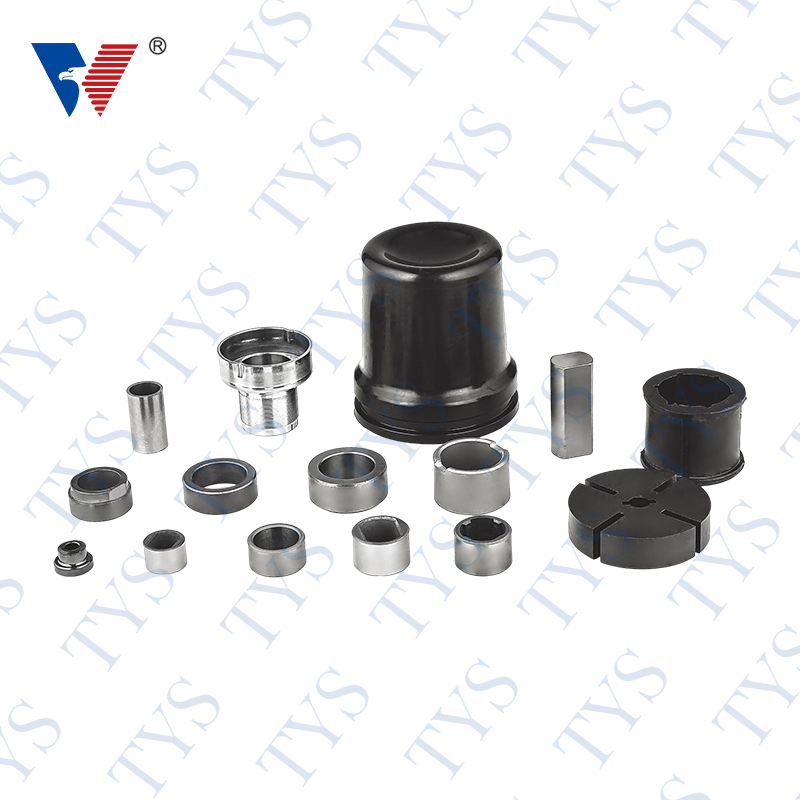
Silicon Carbide, Tungsten Carbide Technical Parameters
Choosing the correct seal material is critical when constructing a rubber seal. It is important to select the right material for the expected temperatures and climates of the application. In addition, it is critical to consider the size of the seal. If the cross-section is too small, the seal may not compress or may cause the connection between the mating surfaces to break. It is also important to avoid too smooth a surface. This may lead to stick-slip effects in dynamic applications.
Rubber sealing materials can be molded or extruded. They are typically shaped into long profiles and strips. They are processed through various thermoforming processes to create the desired shape. The most common method is injection molding, which involves forcing molten rubber through a die. In addition, they can be baked in the same way.
There are several different rubber compounds with different maximum temperature limits. If the material is exposed to extreme temperatures, it can cause cracking or permanent deformation. In order to choose the best seal material for your application, it is important to know the maximum temperature limit. The material should also be chosen based on the length of time that it will be exposed to the environment. If the temperature is too low, the material can be damaged and will not be able to hold up to the deformation pressure. In addition, if the seal is exposed to a temperature higher than the maximum limit, it can cause the material to shrink, which could result in leakage.
When designing a seal, it is important to consider the surface finish of the rubber material. This can affect the fluid containment of the fluid power application. In addition, it is a good idea to have a symmetrical construction to reduce assembly times.
It is also important to take into consideration the pressure that the seal will need to withstand. Depending on the seal, it can be made from rubber or plastic. When customizing the seal, it is also important to account for friction. If the seal will be used to provide a sliding connection, then the coefficient of friction is a critical factor. The seal should be designed with enough elasticity to withstand pressure.
Sealing applications can require a closing force of up to 20 pounds. During the process of compression, the seal may be permanently deformed. The rubber will return to its original shape when the stress is released. This is known as a compression set. It can occur during the production of the seal, or during a test.
If the seal is to be subjected to a large amount of force, the seal's memory function will need to be tested. It is not a universal test, but a company should use the test that they think is appropriate for their application. The Rubber Group uses drawing designations from the Association for Rubber Products Manufactures to help determine the performance requirements for a particular seal.
There are many different industries that employ rubber seals. These include medical, food, and pharmaceutical. They are a versatile product that can offer a quality solution to sealing problems. They are available in a variety of sizes and can be customized to meet your needs.
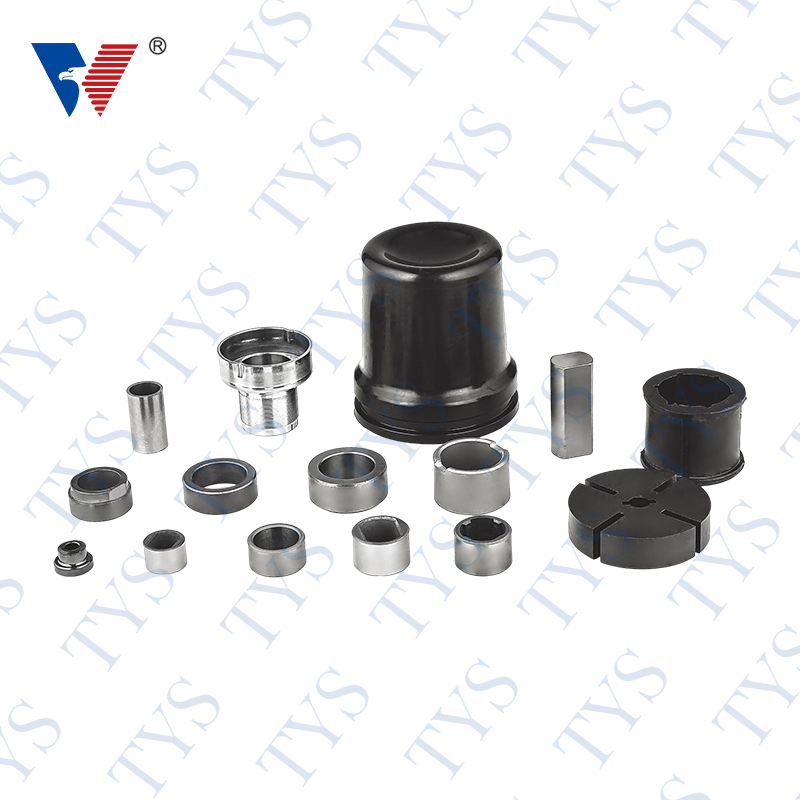
Silicon Carbide, Tungsten Carbide Technical Parameters
Item |
Unit |
Parameter |
|||
SSIC |
SSIC+G |
SSIC+V |
SSIC+M |
||
Voume Density |
g/cm |
≥3.10 |
≥2.80~3.05 |
≥2.95 |
≥2.70 |
%Porosity% |
% |
≤0.2 |
≤0.5 |
≤5 |
≤5 |
Hardness |
HRA/HS |
≥92(HRA294) |
≥91(HRA294) |
||
Bending Strength |
MPa |
≥400 |
≥190 |
≥150 |
≥120 |
Elastic Modulus |
GPa |
≥418 |
≥350 |
≥325 |
≥195 |
Compressive Strength |
MPa |
>2500 |
>1600 |
>1500 |
>900 |
Thermal Expansion Coefficient |
10/℃ |
4 |
3.0 |
2.6 |
2.5 |
Content of Sic |
% |
≥98 |
≥92 |
≥97.5 |
≥90 |
Temperature |
℃ |
1400 |
1400 |
1400 |
1400 |