Enhancing Industrial Flexibility and Reliability with Full Wave Rubber Bellows
Author:admin Date:2023-07-07
In the realm of industrial engineering and mechanical systems, the quest for optimal performance, longevity, and reliability is a continuous pursuit. One key component that has emerged as a critical solution for achieving these goals is the full wave rubber bellows. These ingenious devices offer unmatched flexibility, durability, and resistance to various environmental factors, making them an essential choice for a wide range of applications.
Full wave rubber bellows are flexible, accordion-like components made from high-quality rubber or elastomeric materials. They are specifically designed to absorb thermal expansion, mechanical vibrations, misalignments, and noise in various mechanical systems. The unique construction of these bellows allows them to expand and contract while maintaining a hermetic seal, effectively protecting the internal components from external contaminants.
Features and Benefits
1. Flexibility: Full wave rubber bellows excel in accommodating axial, lateral, and angular movements. Their accordion-like design enables smooth expansion and contraction, making them ideal for applications where constant motion and flexibility are required.
2. Durability: The rubber materials used in manufacturing these bellows are highly resilient and capable of withstanding extreme temperatures, harsh chemicals, and abrasive environments. They provide exceptional resistance to corrosion, UV radiation, ozone, and moisture, ensuring longevity and reliability in demanding conditions.
3. Vibration and Noise Dampening: Full wave rubber bellows absorb and dissipate vibrations, reducing the transfer of mechanical noise and disturbances to the surrounding equipment or structures. This feature is particularly advantageous in machinery, automotive, and aerospace applications, where minimizing noise and vibrations is crucial for performance and operator comfort.
4. Thermal Expansion Compensation: In systems where temperature fluctuations occur, such as pipelines or exhaust systems, full wave rubber bellows play a vital role in compensating for thermal expansion and contraction. By absorbing the expansion forces, these bellows prevent undue stress on the system, reducing the risk of leaks, fractures, or other forms of damage.
Applications
1. Automotive Industry: Full wave rubber bellows are commonly used in exhaust systems, suspension systems, and drivetrains to absorb vibrations, compensate for thermal expansion, and enhance overall durability.
2. HVAC Systems: In heating, ventilation, and air conditioning systems, these bellows aid in absorbing thermal expansion and contraction, reducing noise transmission, and compensating for misalignments between ducts and equipment.
3. Aerospace and Aviation: Full wave rubber bellows find applications in aircraft engines, landing gear systems, and environmental control systems, where they provide vibration isolation, compensate for thermal expansion, and maintain airtight seals.
4. Industrial Piping: In industrial settings, these bellows are used to connect pipes and compensate for thermal expansion, misalignments, and vibrations in chemical plants, refineries, and power generation facilities.
Full wave rubber bellows are flexible, accordion-like components made from high-quality rubber or elastomeric materials. They are specifically designed to absorb thermal expansion, mechanical vibrations, misalignments, and noise in various mechanical systems. The unique construction of these bellows allows them to expand and contract while maintaining a hermetic seal, effectively protecting the internal components from external contaminants.
Features and Benefits
1. Flexibility: Full wave rubber bellows excel in accommodating axial, lateral, and angular movements. Their accordion-like design enables smooth expansion and contraction, making them ideal for applications where constant motion and flexibility are required.
2. Durability: The rubber materials used in manufacturing these bellows are highly resilient and capable of withstanding extreme temperatures, harsh chemicals, and abrasive environments. They provide exceptional resistance to corrosion, UV radiation, ozone, and moisture, ensuring longevity and reliability in demanding conditions.
3. Vibration and Noise Dampening: Full wave rubber bellows absorb and dissipate vibrations, reducing the transfer of mechanical noise and disturbances to the surrounding equipment or structures. This feature is particularly advantageous in machinery, automotive, and aerospace applications, where minimizing noise and vibrations is crucial for performance and operator comfort.
4. Thermal Expansion Compensation: In systems where temperature fluctuations occur, such as pipelines or exhaust systems, full wave rubber bellows play a vital role in compensating for thermal expansion and contraction. By absorbing the expansion forces, these bellows prevent undue stress on the system, reducing the risk of leaks, fractures, or other forms of damage.
Applications
1. Automotive Industry: Full wave rubber bellows are commonly used in exhaust systems, suspension systems, and drivetrains to absorb vibrations, compensate for thermal expansion, and enhance overall durability.
2. HVAC Systems: In heating, ventilation, and air conditioning systems, these bellows aid in absorbing thermal expansion and contraction, reducing noise transmission, and compensating for misalignments between ducts and equipment.
3. Aerospace and Aviation: Full wave rubber bellows find applications in aircraft engines, landing gear systems, and environmental control systems, where they provide vibration isolation, compensate for thermal expansion, and maintain airtight seals.
4. Industrial Piping: In industrial settings, these bellows are used to connect pipes and compensate for thermal expansion, misalignments, and vibrations in chemical plants, refineries, and power generation facilities.
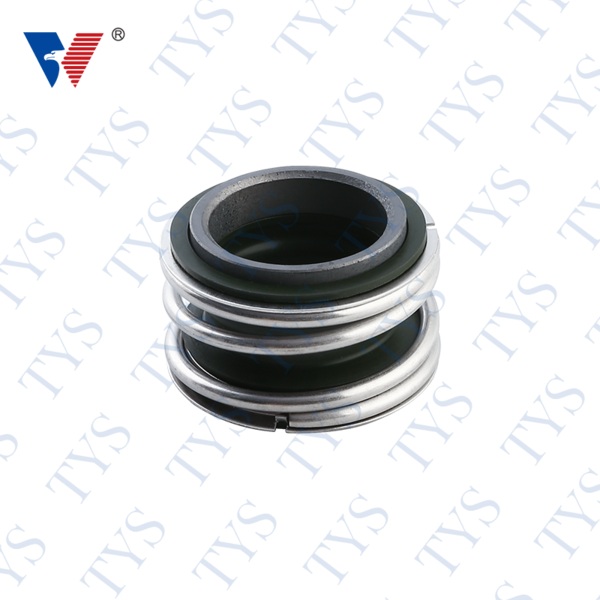